Each airline has its own way of determining when it’s time to retire an aircraft. A good example of this is the fate of the McDonnell Douglas DC-9 fleet Delta Air Lines inherited after its 2008 merger with Northwest Airlines. While most carriers retired their DC-9s (which first started flying in 1965) in the 1990s, Northwest chose to keep flying them. But after the merger, Delta began phasing them out, with the last one retired in May 2014.
But how, exactly, do you retire a decommissioned aircraft? What happens when an aircraft comes to the end of its service life? Where do its myriad parts go after a decommissioning?
We take a look at the process, and learn how Panasonic Avionics has a system in place to recycle IFEC systems on those retiring aircraft more efficiently.
‘Economic Obsolescence’
George Hamlin is President of the Fairfax, Virginia-based Hamlin Transportation Consulting, a firm that advises on airline and aircraft economics and fleet-planning issues. He has spent more than 40 years in the industry, working for companies including Airbus, Lockheed Martin, TWA and Texas International Airlines.
There are several reasons why an airline makes the decision to decommission an aircraft, says Hamlin. “Simply put, airlines have fleet-planning processes where older aircraft are rolled out to bring in new ones. It’s about economic obsolescence.”
For example, an airline can decide to go from the Boeing 737 Classic to NextGen to the newest MAX series. “Over time, you don’t want a mixed fleet because it complicates maintenance and pilot training,” says Hamlin. “And you want to keep everything modern and efficient, along with keeping maintenance simple.”
This means that sometimes aircraft are retired before they’ve lived out their full usefulness. Thankfully, decommissioned aircraft typically aren’t scrapped wholesale — meaning there can be life after death for some of their components.
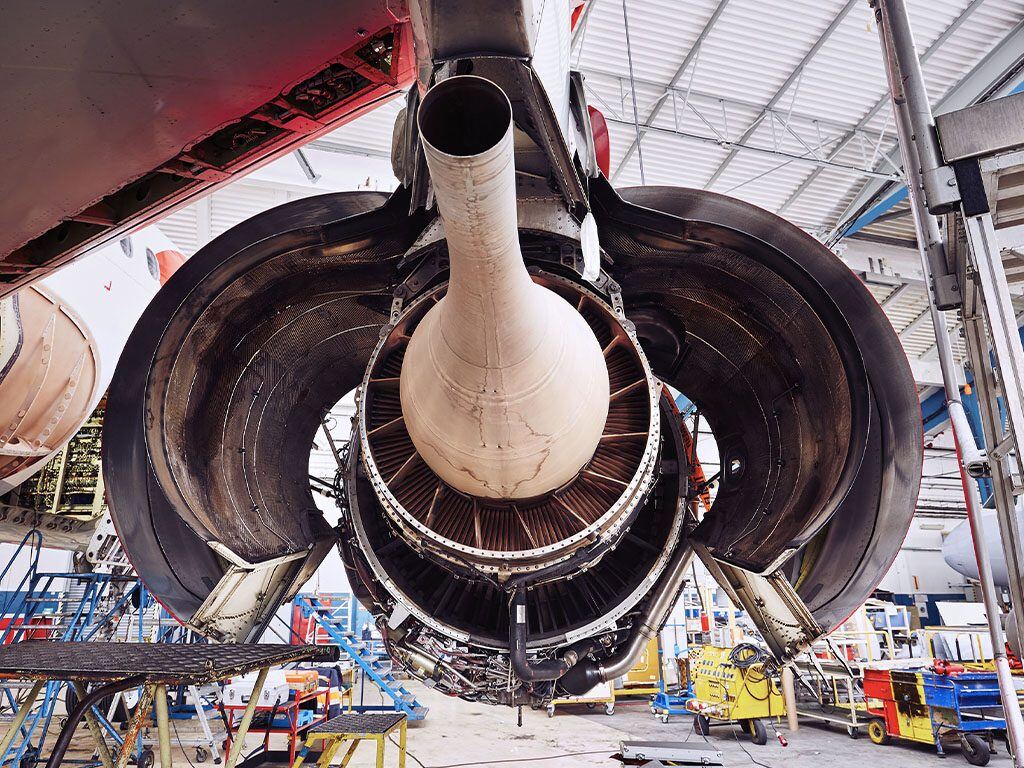
How Aircraft get Stripped
The big question airlines ask is whether an aircraft is worth more alive or dead, continues Hamlin. “When an aircraft is sent for stripping, that means that it no longer has value as a flying entity. But at the end of its physical life, there are still plenty of parts that still have value,” he explains. “These include landing gears, control surfaces, flaps, rudders, doors and engine parts.”
That’s where Shawn Bergquist, a director at Intertrade Limited, comes in. Intertrade is a company that works with aircraft-stripping companies to sell re-certified airframe and engine parts. “Intertrade focuses more on buying parts from companies that are tearing down the aircraft,” he says. “We then buy and sell used aircraft and engines parts to the airlines.”
Bergquist walked through the aircraft-stripping process. “Once the tear-down process is contracted to a third party, an aircraft safety check is performed. It is grounded, panels are removed and then all fluids and hazmat materials are de-puddled,” he says.
Next, the engines are removed, followed by the most desirable parts. “The vendor will then perform a systematic removal of parts, by system,” says Bergquist. In order, this includes:
1.Safety equipment, including things like slides, rafts and batteries;
2. Flight deck and electronics bay avionics;
3. Interior equipment such as passenger seats, class dividers, ceilings, sidewalls, overhead bins, galley ovens, coffee makers, lavatories and IFEC monitors;
4. Auxiliary power units (APUs);
5. Antennas and electrical systems;
6. Hydraulics and pneumatics;
7. Flight controls and doors; and
8. Flight deck cut-out, if applicable.
“Wheels, brakes and landing gear are usually last to be removed, then the aircraft hull is disposed of,” says Bergquist. “The entire process takes about two to three weeks.”
Almost 95 percent of an aircraft can be recycled, says Bergquist. “The easiest parts to recycle are engines, APUs, avionics and electronics, actuators, hydraulics and pneumatics, wheels, brakes, landing gear and flight controls. Recycling has become more important because it’s a more cost-effective means for operators to maintain and service their fleets.”
“When an aircraft is sent for stripping, that means that it no longer has value as a flying entity. But at the end of its physical life, there are still plenty of parts that still have value such as landing gears, control surfaces, flaps, rudders, doors and engine parts.”
-George Hamlin
President of Hamlin Transportation Consulting
Recycling IFEC Systems
Recycling aircraft parts is one thing. Recycling the electronics that make up the inflight entertainment and communications system is a whole other challenge. That’s especially true today, where rapid changes in the industry and passenger demands for the latest IFEC options have seen airlines replacing their systems more frequently than ever despite the fact that many were originally built to last between 10 and 15 years.
So, what happens to those systems after they are stripped from an aircraft?
First, manufacturers such as Panasonic Avionics try to give the technology a new life by refurbishing the IFE components and putting them back into use with customers who need replacement units for older systems.
If they can’t be repurposed, they get recycled. At Panasonic Avionics, they’re logged into a database called the Green Product Web (GP-Web system) that tracks all the material and substances used in its products, including IFE systems.
“Once you buy a part from one of our supplier bases, they go and register what type of material it’s made of,” says John Hernandez, Supervisor of Green Product Compliance at Panasonic Avionics. “We’re also able to tell our customers if any of our products still has cadmium plating on it or if there’s lead in any of the electronic components via the GP-Web database.”
Cadmium plating, used extensively in aviation and aerospace products, is being phased out because of concerns about its toxicity to the environment. “We make a lot of cables for our airline customers,” says Donna Brunot, a Quality Engineer responsible for Panasonic’s Environmental Management System (EMS), “and let them know if it has cadmium plating because it has to have special handling and recycling. Thanks to the GP-Web, we can give that information to our customers.”
Engineers also use GP-Web when developing new IFE products. “When they select a new part for their design, they first look at the components that we have in our library,” Brunot says. “If they don’t find them in the library, we will find the component. If it’s not compliant, we ask them to select a different one.”
Panasonic Avionics advises airlines — even if they’re not customers — on finding approved suppliers around the world that recycle IFEC parts responsibly, says Brunot. “We have audited these companies and do business with those who recycle at above 92 percent and have a good reputation.”
Ensuring that as many pieces of an aircraft as possible are recycled is a key piece of corporate social responsibility, for both manufacturers and airlines. “We can’t even imagine our products not being recycled,” says Brunot. “The world has limited resources, so they need to be reused as much as possible.”